Loach Engineering
Loach Engineering Inc. designed and manufactured custom automation machinery, specializing in the printing industry. The company underwent several iterations as industries and technologies changed. During Loach’s eighty years of manufacturing, drafting tables, slide rules, milling machines, and relay boards evolved into CAD systems and 3D modeling, calculators, numerical control machining and programmable controllers.
Originally founded by tool and die maker S.W. (Bill, or Smiley) Loach (1899 – 1980) during the Great Depression, the Toronto based manufacturer serviced large local companies such as The Goodyear Tire and Rubber Company, and Weston’s Bakeries. The first factory was on Roselawn Avenue, west of Bathurst Street.
Bill Loach’s son, Roy (1928 – 2020), joined the company after graduating from Mechanical Engineering at the University of Toronto in 1952. Roy hadn’t planned on joining his father’s firm, but when his father Smile presented son Roy with business cards with his name on them, and the new company name – S.W. Loach & Son Ltd. – it was a done deal.
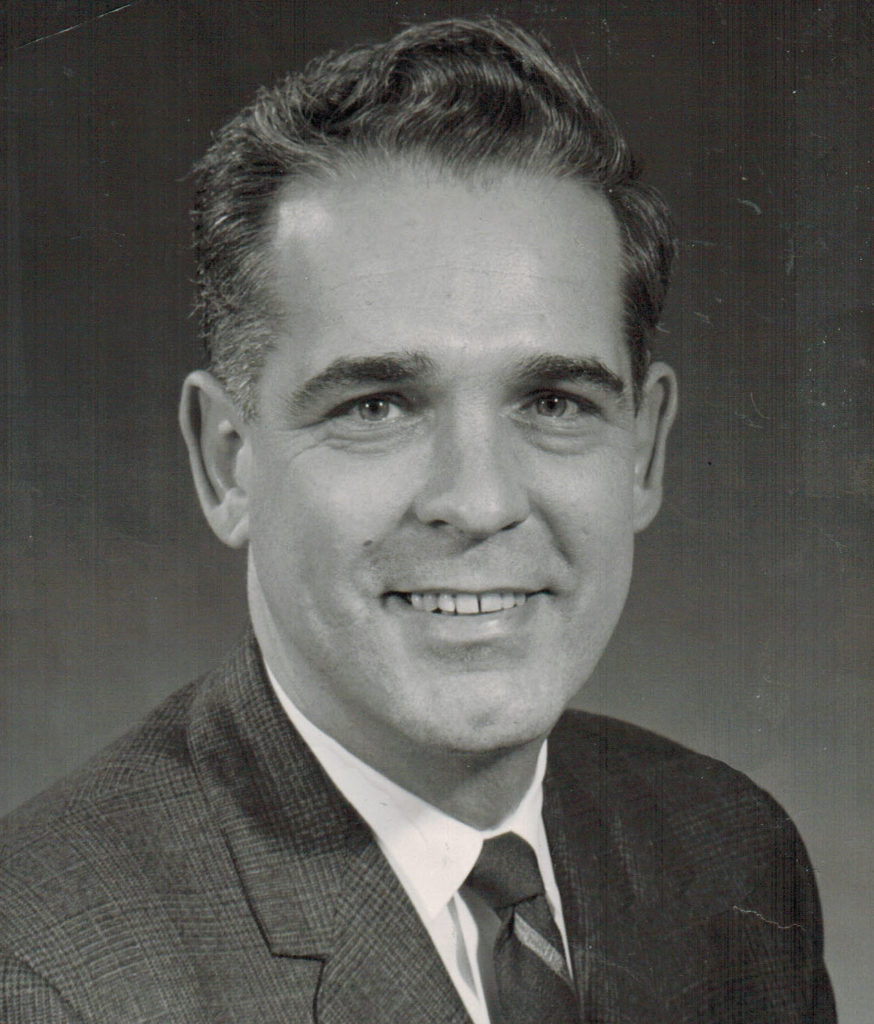
Soon after, one of Loach’s products, a wire-turn conveyor, caught the eye of the Sheridan Company of New York, a major producer of book binding and newspaper inserting machinery. Loach became a supplier to Sheridan, and Loach’s book stackers, trimmer feeders, laydown conveyors, and turns were shipped to many of the largest printing companies in the world. Loach needed more space and built a factory at 106 Howden Road in Scarborough in the east end of Toronto.
The Sheridan Company, recently purchased by Harris-Intertype, bought one-half of S.W. Loach & Son in 1963, and the company was renamed Sheridan-Loach Ltd. In 1970, Harris bought all of Sheridan-Loach, closed the Toronto shop, and moved the manufacturing to their factory in Champlain, N.Y.
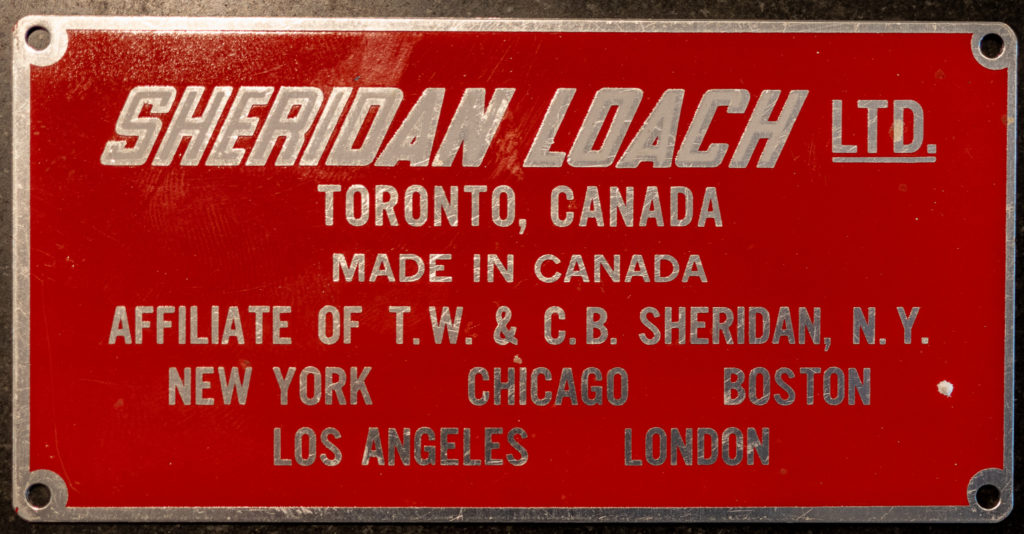
Bill (Smile) Loach retired and devoted his time to building replica model steam engines, fly-fishing, and his three grandchildren.
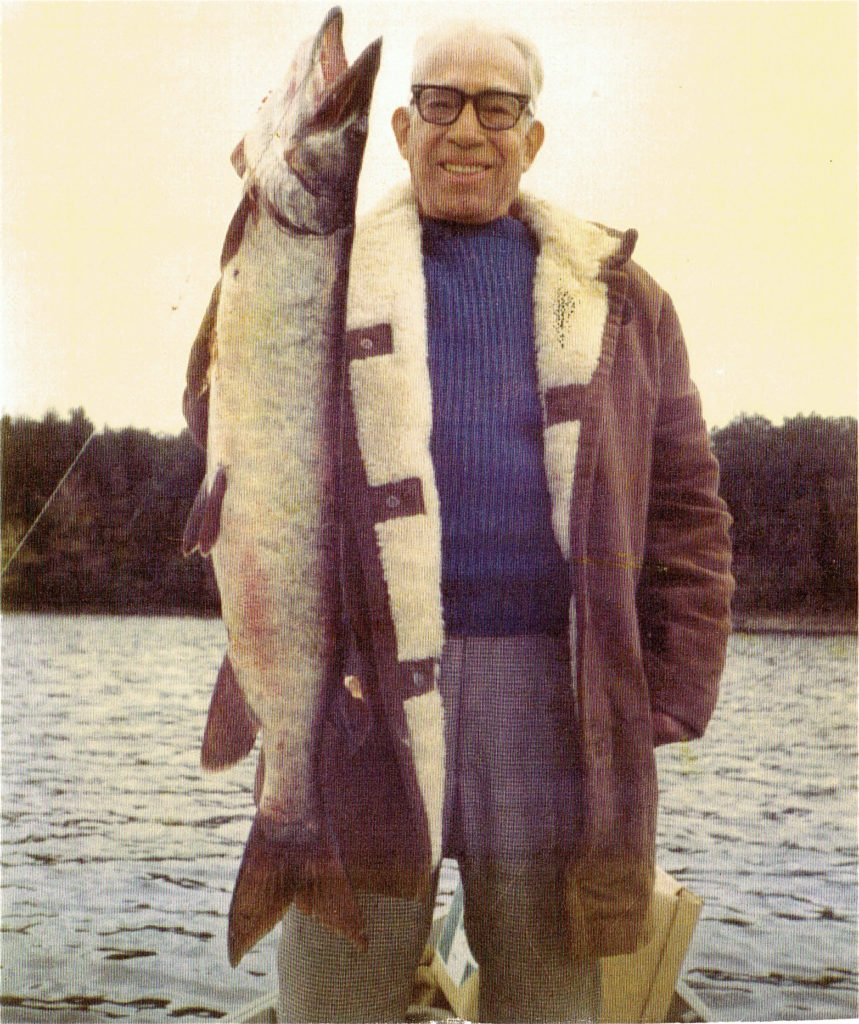
Roy was offered a position at Harris’s engineering office in Easton, Pennsylvania. The whole family, Roy, his wife Marny and their children, John, Keith and Claire, visited Easton where Roy and Marny were aggressively wooed and shown around town. The homes were huge – much better bang-for-the-buck than what they could afford in Toronto. It would have been a wonderful opportunity for Roy and Marny, but Roy declined because his two sons – John and Keith – would soon have been eligible for the Vietnam War draft.
Instead, Roy became the Canadian sales representative for Harris / Sheridan. Roy worked out of the Harris office on Lesmill Road in Toronto’s Don Mills.
Missing engineering, Roy moved on in 1976 and started Loach Engineering Ltd. as a commissioned sales agent for Harris / Sheridan. He borrowed money against his house to set up the company and get through the first few lean months. Working from home, Roy provided consulting engineering services to Canadian printers, and managed Technical Aids and Services for the Handicapped (TASH) at Sunnybrook Hospital.
Roy’s son John joined his father in 1980 after earning a Mech Eng degree from Univ of Toronto. Roy and John began returning to the company’s roots – designing and manufacturing industrial machinery. They moved out of Roy’s house, rented an office at The Fitness Institute, and eventually opened a small machine shop at 2600 John Street, just north of Toronto.
Roy and John hired a previous draftsman of Roy’s, Jim Procter, and, with a contact from a friend of Roy’s from Harris, Richmond Chandler, designed and built a meat patti cartoning machine for the supplier to McDonalds. Although the project failed, it was very valuable experience for young engineer John. Commission sales and a few orders for book stackers and conveyors from Harris kept the company afloat.
Younger brother Keith Loach joined the company in 1985 after earning a Bachelor of Music from University of Toronto.
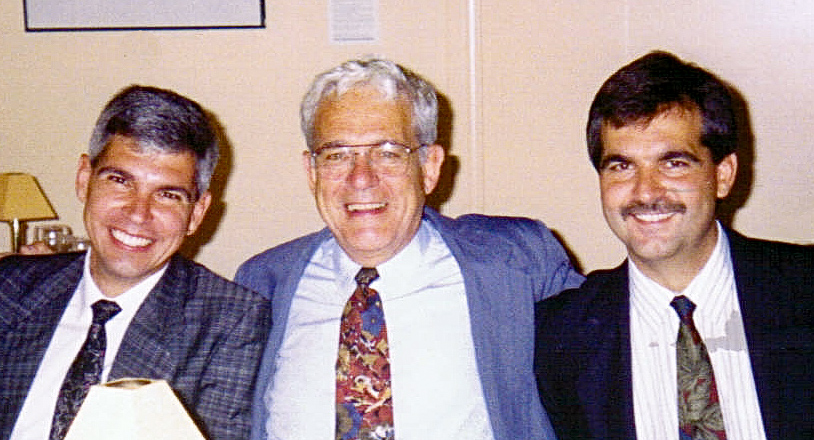
The machine design business was changing fast. Computers were being introduced for computer-aided-design (CAD) and programmable logic controllers (PLC). Loach Eng embraced these challenges, and manufacturing and software development at the firm expanded.
In 1987 the company split into two. Keith partnered with Chris Tremblay to form Loach Systems Inc. Roy continued to represent Harris / Sheridan in Canada as an employee of Loach Systems. Keith and Chris expanded the company to supply the packaging industry with shrinkwrap machines from Sitma (Italy) and plastic film wrap from Cryovac.
John’s company, the newly formed Loach Engineering Inc., moved to Kingston, Ontario, and opened a large factory on Hickson Avenue (with a huge mortgage and line of credit from TD Bank). John and his wife Patti bought a home near Queen’s University and found new schools and friends for their three young boys.
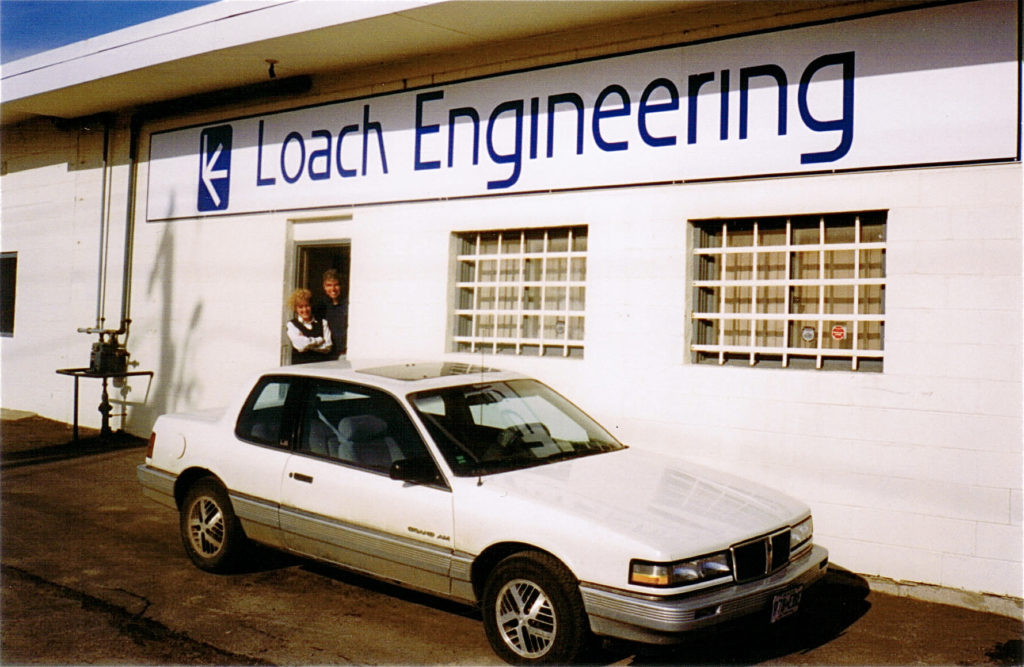
Patti took over managerial duties (inventory control, purchasing, receiving, payroll and bookkeeping). Patti, along with a team of welders, millwrights, painters, assemblers, electricians and hardware and software engineers, allowed John to concentrate on sales and engineering. Together, this team created machinery for customers that included R.R. Donnelley (catalogues), Arcata Graphics (pocketbooks, Readers Digest, Harlequin), Quebecor (magazines), Rand McNally (encyclopedias), and Toronto Star and Globe & Mail (insert feeders).
John and Keith (and their respective companies) were the beneficiaries of Roy’s four decades of experience and relationship building with major players in the printing industry. Happily, at the end of his career, Roy closed one of the largest newspaper mailroom equipment contracts ever received by the Sheridan Company, a huge order for the new Toronto Star production facility in Woodbridge, Ontario. This provided a comfortable retirement for Roy and Marny.
Throughout their lives, Roy and Marny had been very active as volunteers with Rotary International and Bloorview Children’s Hospital (formerly Ontario Crippled Children’s Centre). At Bloorview, Roy was known as the ‘Toy Doctor’, modifying toys and tools to address childrens’ individual physical requirements.
In 1991, a disastrous project with a major printer landed Loach Engineering in deep financial trouble. The monies owed to the customer, the bank, and suppliers far exceeded Patti and John’s personal guarantee against their house.
Fortunately, the customer agreed to allow Loach Engineering two years to resell the machines to other customers. Knowing this, the bank held off. Patti gradually paid back all of the suppliers, and LoachEng sold all of the machines to printers in the United States. A huge stressful period, but company failure was thankfully avoided.
Luckily, around the same time, Loach was contacted by Hank Boulton of Involvo North America. Hank had met John at Pack Expo, an annual packaging trade show in Chicago. Hank had noticed a small machine that Loach Engineering had on display, and Hank and John chatted about machine design capabilities and long-distance running (mostly long-distance running). Hank represented companies specializing in the paper manufacturing industry, and had recently installed a cheque packaging machine at the John H. Harland company in Atlanta, Georgia. Harland needed more of these machines for their plants across the United States, but the Atlanta machine was troublesome. Hank felt that Loach may be able to design a better machine, and secured an order from Harland for a Loach-designed ‘Close-Out System’. The future changed for the better.
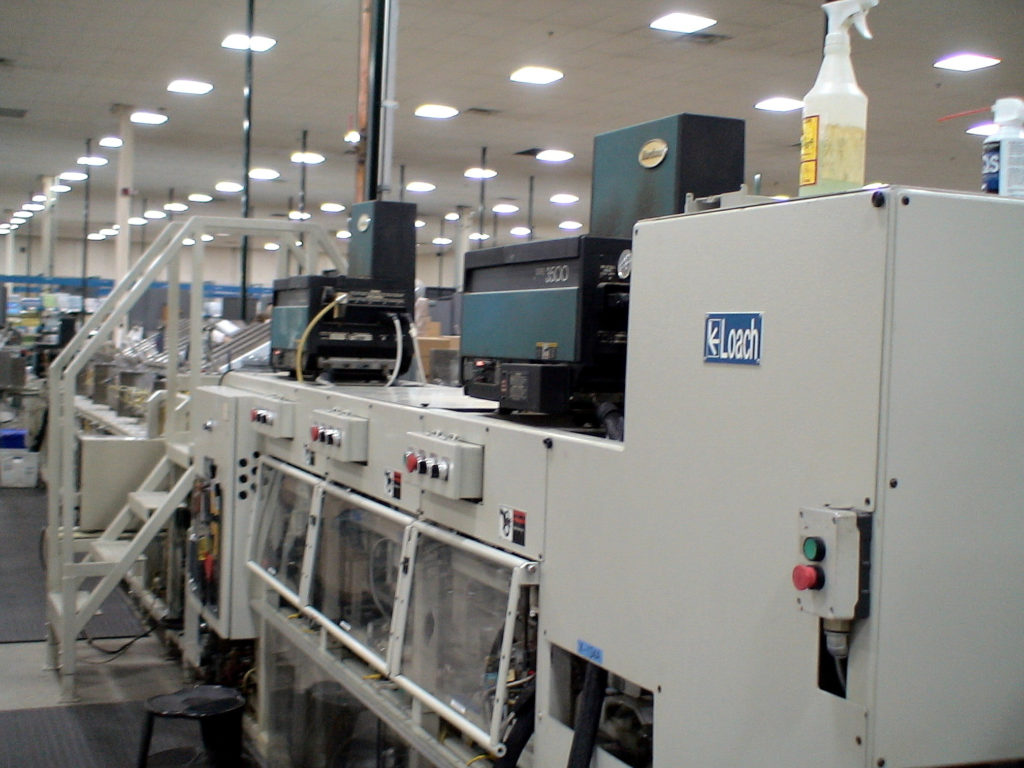
Over the next ten years Loach supplied over forty of these large packaging machines to the check printing industry, and additionally designed and manufactured the mail sortation equipment for these plants. The Kingston plant was extremely busy. At its peak, forty people worked over three shifts a day, and the local Kingston suppliers of automation equipment posted record sales to Loach.
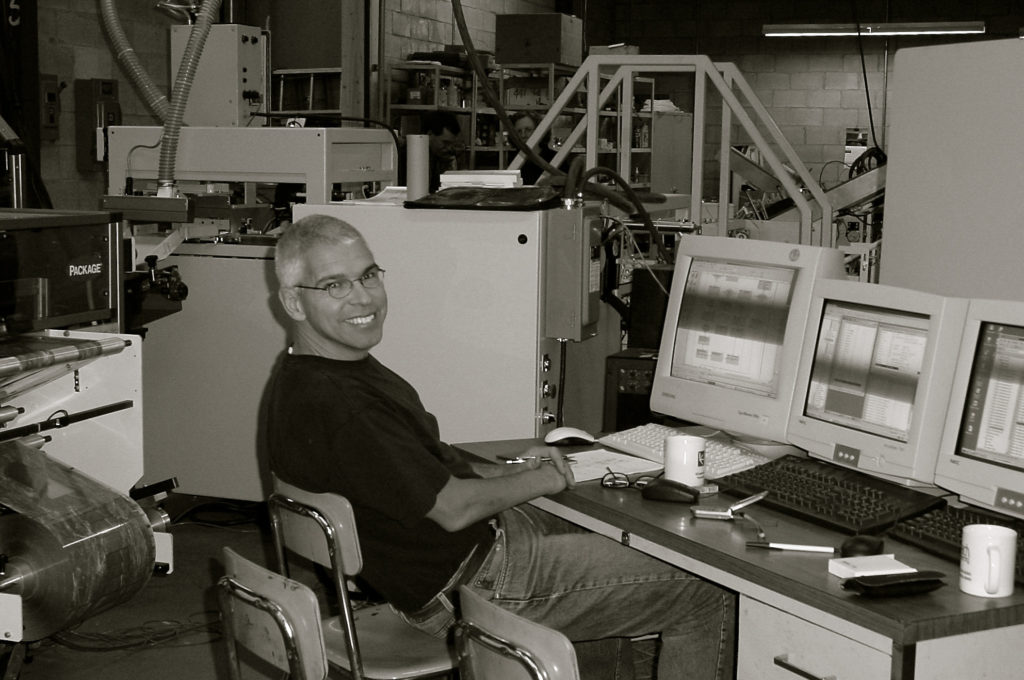
When the available cheque printing industry’s machinery needs were filled, John and Patti – with extremely heavy hearts – decided that the risks of developing another line of equipment to maintain production were too high. On May 2, 2003, they advised their employees, some of whom had been with them from the beginning, that Loach Engineering was ceasing all operations. Six weeks later, Patti and John handed over the 141 Hickson Avenue keys to its new owner, Kingston Anchors.
After Roy’s retirement in 1994, Loach Systems continued as the Canadian sales agent for AM Graphics (originally Sheridan/Harris) closing large turnkey mailroom and bindery orders across Canada, including systems at the Ottawa Citizen, Windsor Star, Calgary Herald, St. John Telegraph Journal, Toronto Sun, Photo Engravers, and St. Joseph Printing.
Shrink Packaging Ltd. (SPL Systems) was established in 1991 under the same ownership structure as Loach Systems to focus on the packaging industry. SPL grew over the years to become the leading independent film and machinery supplier in Ontario. After reaching revenue of $10 million and supporting a staff of fifteen in sales and service, SPL Systems was sold to a friendly competitor in 2004.
Since 2003, John has focused on music (playing trumpet and recording musicians in the studio he built in the kitchen of the home he shares with Patti), robotics (volunteer teaching at local schools), photography, and model railroading. In addition, he has designed and hosts a number of websites and blogs for friends.
Patti returned to her first love – music – and has enjoyed working and performing with singers and actors across Canada and around the world. The acquisition of a Steinway B grand piano in 2001 was a game-changer not only for Patti, but for John as well, since it has been a feature of the more than fifty ‘Jazz In The Kitchen‘ concerts they have hosted in their home.
Additionally, John and Patti love good food, traveling, making music together, cycling (recumbent trikes), and spending time with their three sons and extended families.